Robotic Winding Integration
Dec 2020 – Jan 2021
Category: Robotic Construction, Computational Design
Director: Michael Weinstock
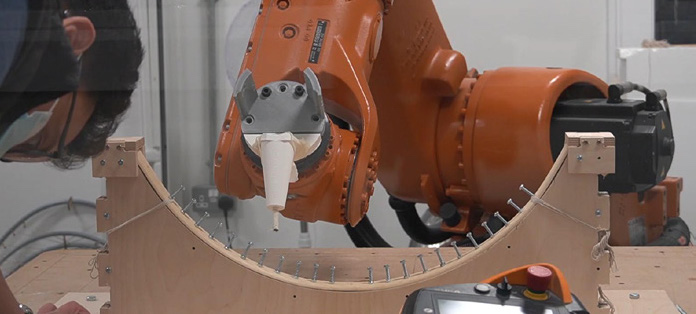
This project stands at the intersection of architecture, computational design, and material engineering, aiming to harness advanced fabrication techniques for creating innovative architectural structures. The methodology integrates digital design processes with physical prototyping to ensure the feasibility and efficacy of the proposed pavilion design.
- Through computational aggregation tools, the project explores innovative approaches to volumetric population of components over global surfaces.
- The integration of robotic winding techniques in architectural pavilion design, enabling precise fabrication of complex geometries and active bending elements for enhanced structural stability.
- The project refines design solutions based on diverse criteria, including density of components, structural stability, shadow analysis, and solar radiation management
Component Scale Design
At the Component scale, the project focuses on selecting materials and active bending elements conducive to Robotic Winding. Wood is chosen for its orthotropic properties, facilitating active bending under applied forces. Finite Element Analysis (FEA) is utilized to evaluate various winding patterns, ensuring structural stability and mitigating deformations resulting from active bending. The selection and refinement of winding patterns constitute essential steps in achieving stability and functionality at the Component level.
Global Scale Design
Moving to the Global scale, the design process involves the parametric derivation of a surface within specified dimensions. Employing anthropometric parameters, such as habitable volume, scale, and accessibility, alongside structural efficiency and environmental optimization criteria, a self-supporting domical structure is formulated. Multi-objective parametric tools aid in optimizing the global geometry for both human occupancy and environmental considerations, particularly solar radiation management and shade provision.
Regional Scale Design
At the Regional scale, the focus shifts to volumetric population of components over the global surface, facilitated by computational aggregation tools. Rules of joinery between components guide the aggregation process, considering factors such as density, visual transparency, and spatial quality. Multi-objective optimization further refines the selected aggregation, ensuring structural stability and shadow analysis based on location data. The introduction of a third winding pattern regionally enhances both sun-shade effectiveness and structural integrity.
Prototyping and Validation
The final stage encompasses physical prototyping, validating the digital models through fabrication and testing. Robotic arms and table jigs are employed to execute the proposed winding patterns, allowing for a comparative analysis between the physical prototype and the digital model. Structural stability and deformations resulting from active bending forces serve as key criteria for assessing the efficacy of the design.